At Technologies International, Inc. we work daily with food companies, helping them implement new ERP systems, unify business processes to control costs and helping them meet changing governmental regulations on the national, state and local levels.
By far the biggest issue we encounter is helping businesses with lot traceability and the ability to quickly and competently institute a product recall if necessary.
We have partnered with SYSPRO software and have found that its ERP system offers advanced lot trace capabilities for food manufacturers and distributors and it gives our clients complete visibility of their supply chains every step of the way-from farm to store shelves and beyond.

No food company wants to go through a product recall but all of them have to be prepared for one and with SYSPRO’s product recall system, the entire process can be quickly initiated and launched, meeting all government regulations surrounding food safety.
Recall Management
With the latest version release, SYSPRO’s Product Recall capabilities has been expanded to allow any traceable parent item (Lot or Serial traceable) that has been receipted into stock by any means, to be easily identified. The ability to identify where any raw ingredient has been used has been added to the identification logic.
Product Recalls
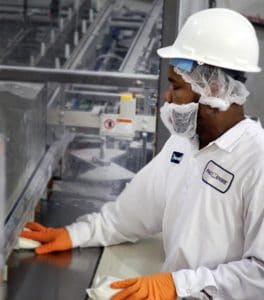
SYSPRO Product Recall allows you to perform a full product recall quickly and efficiently.
With detailed information related to a suspect product available at the touch of a button, you can rapidly identify and retrieve potentially defective goods from customers using your organization’s Product Recall System.
Accelerate the Time to Completion of Your Product Recalls: With quick and easy access to all of the key product information recorded in the purchase, production, packaging, sale, distribution and delivery of a product in SYSPRO’s Product Recall capability, you can swiftly trace and quarantine stock which is defective, be it spoiled, damaged, hazardous or of inferior quality.
Improve Governance and Drive Compliance: At Technologies International, Inc. we work with our customers to help build and support quality and food safety systems.
We’ve developed an ERP driven labeling solution to pull information directly from the business system to create labels that are compliant, reduce the need for multiple templates and eliminates errors caused by constantly keying and re-keying data into labeling software.
It’s all part of the plan to develop and maintain a full traceability and recall system policies, plans and procedures – improving internal governance and driving compliance.
Continually Test and Improve Your Traceability System: It’s not enough to build a system and only test it during implementation. Forward thinking food companies regularly perform mock recalls that enable businesses to test and continually improve on the effectiveness and robustness of their traceability systems, increasing the likelihood of a quicker time to completion in the event of an actual product recall.
Remain Compliant and Meet Regulatory Reporting Requirements: By recording and documenting all of the steps and activities that occur in the mock recall, you can test and report on your ability to achieve the time to completion and highlight the ability of your traceability system to meet regulatory requirements in the case of an actual recall.
Mitigate the Reputational Risks Associated with Recall: The ability to execute a recall process within the two to three hours required decreases the likelihood of a food incident resulting in significant public health issues – safeguarding public health, which is the organization’s primary responsibility.
Being able to recall a product seamlessly will also mitigate the possible reputational and financial risks of a recall such as litigation, loss in customer loyalty, shareholder confidence and even bankruptcy.
Creating a robust lot traceability system and holding regular mock recalls will improve the recall process, and develop supplier and customer confidence as most food incidents will be contained and lead to withdrawals as opposed to a full product recall.
If your company is struggling with traceability and recall planning issues Technologies International, Inc. can help. We’ve been working with California food and beverage companies for more than 20-years.
Call us today at (909)-614-1416 or email us at sales@tech-intl.com and let’s talk.